API 607 vs API 608
Industrial?environments?dealing?with?flammable?and?combustible?materials?require?stringent?safety?measures,?especially?concerning?valve?performance?under?fire?conditions.?This?is?where?the?American?Petroleum?Institute?(API)?standards,?specifically?API?607?and?API?608,?come?into?play.?These?standards?provide?a?framework?for?testing?and?certifying?valves?for?fire?safety,?ensuring?their?integrity?in?extreme?situations.
What is API 607?

API 607 outlines the fire test requirements for quarter-turn valves with soft seats, commonly used in hydrocarbon processing, chemical plants, and other industries. The focus is on preventing internal leakage when the valve is subjected to a standardized fire test.
Key aspects of API 607
Scope:?This?standard?applies?to?quarter-turn?valves,?including?ball,?plug,?and?butterfly?valves,?with?soft?seats?made?from?elastomers?or?polymers.
Test?Conditions:?API?607?mandates?a?demanding?fire?test?where?the?valve?is?exposed?to?a?temperature?of?1400°F?(760°C)?for?30?minutes.?During?the?test,?the?valve?is?pressurized?with?a?test?medium,?typically?water?or?air,?and?leakage?is?carefully?monitored.
Acceptance?Criteria:?To?pass?the?API?607?fire?test,?the?valve?must?demonstrate?minimal?internal?leakage?through?the?seat?and?stem?during?and?after?the?fire?exposure.?The?standard?defines?specific?permissible?leakage?rates.
What is API 608?
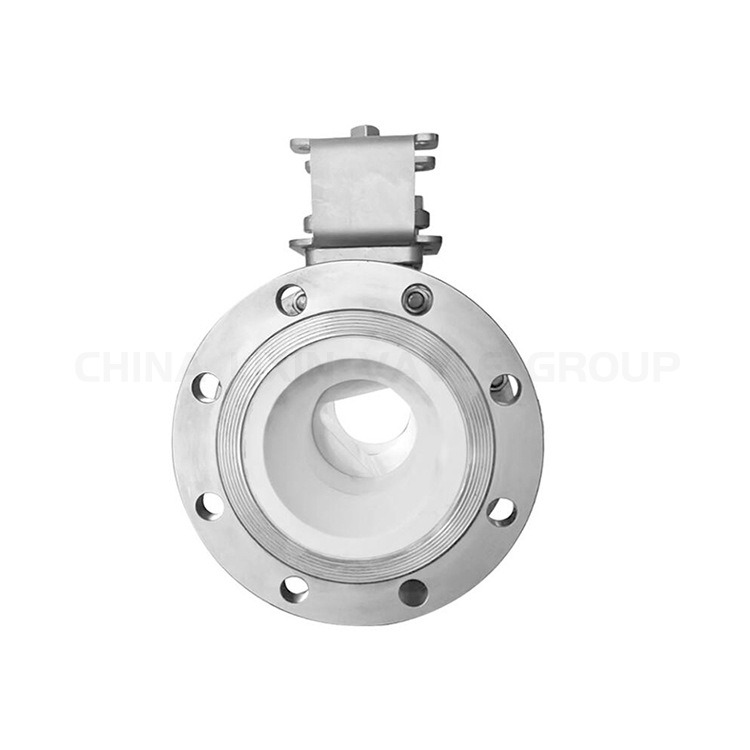
While API 607 covers a broader range of quarter-turn valves, API 608 specifically focuses on fire testing requirements for metal ball valves. This standard emphasizes both internal and external leakage during the fire test, making it stricter in its assessment. API 608 Ball Valve
Key aspects of API 608
Test?Conditions:?Similar?to?API?607,?the?valve?is?subjected?to?a?fire?test?at?1400°F?(760°C)?for?30?minutes.?However,?API?608?includes?an?additional?requirement?for?external?leakage?testing.
Leakage?Assessment:?API?608?requires?monitoring?for?both?internal?leakage?through?the?seat?and?external?leakage?through?the?stem?packing?and?body?seals.
Acceptance?Criteria:?Passing?the?API?608?fire?test?requires?adhering?to?more?stringent?leakage?limits?for?both?internal?and?external?leakage?compared?to?API?607.
API?607?vs?API?608
Feature | API 607 | API 608 |
---|---|---|
Scope | Fire test standards for valve performance in fire conditions. | Standards for design, inspection, and testing of metal-seated ball valves. |
Valve Types | Soft-sealed valves, e.g., ball and butterfly valves. | Metal-seated ball valves, including cast and trunnion. |
Purpose | Enhance safety by ensuring valves can halt or control fluid flow in fire scenarios. | Ensure valve performance under various pressure and temperature conditions. |
Testing Conditions | Simulates fire scenarios to test valve integrity and function. | Tests under normal operating conditions to assess pressure handling and sealing. |
Certification | Requires valves to withstand direct flames and function post-test. | Valves must meet specific operating pressures and temperatures post-testing. |
Industry Application | Used in industries where fire safety is critical, such as oil, gas, and chemicals. | Primarily used in the oil and gas sector for fluid handling. |
Testing Process | Includes exposure to flames and thermal cycles. | Involves rigorous pressure and sealing tests. |
Design Focus | Primarily on maintaining sealing properties during and after fire exposure. | On durability and performance in varying operational conditions. |
API?607?Fire?Safe?Test?Procedure
Test Step | Description |
---|---|
Valve Preparation | The valve is prepared by removing any non-essential components and ensuring the sealing surfaces are clean and free from debris. |
Test Setup | The valve is mounted in a dedicated test fixture and connected to a pressure source and a leakage collection system. |
Initial Pressure Test | A preliminary pressure test is conducted before fire exposure to verify the valve’s initial integrity and sealing capacity. |
Fire Exposure | The valve is subjected to a standardized fire test using a furnace or a calibrated burner, with temperature carefully controlled for 30 minutes. |
Leakage Monitoring | Internal leakage through the seat and stem is collected and measured during and after the fire test. |
Test Inspection | After fire exposure, the valve undergoes a visual inspection for signs of damage, deformation, or deterioration. |
API?608?Fire?Safe?Test?Procedure
Test Step | Description |
---|---|
Valve Preparation | Similar to API 607, the valve is prepared by removing any non-essential components and ensuring the sealing surfaces are clean. |
Test Setup | The valve is mounted in a test fixture, connected to a pressure source, and equipped with collection systems for both internal and external leakage. |
Initial Pressure Test | An initial pressure test is conducted to verify the valve’s integrity before the fire test. |
Fire Exposure | The valve is exposed to a standardized fire test at 1400°F (760°C) for 30 minutes. |
Leakage Monitoring | Both internal and external leakage are carefully monitored and measured throughout the test. |
Test Inspection | A thorough visual inspection is performed to check for any damage, deformation, or deterioration caused by fire exposure. |
Significance?of?API?607?and?API?608?in?Industrial?Safety
API 607 and API 608 play a vital role in ensuring the reliability and safety of valves in fire environments. By adhering to these standards, manufacturers can demonstrate the fire-resistant capabilities of their valves, providing a higher level of assurance to plant operators and engineers. This peace of mind translates into increased operational safety, reduced risk of fire-related incidents, and compliance with industry best practices and regulatory requirements.
Benefits?of?Utilizing?API?607/608?Certified?Valves
Benefit | Description |
---|---|
Enhanced Safety | Certified valves offer greater fire-resistant capabilities, reducing risks and protecting personnel. |
Compliance with Industry Standards | Ensures adherence to recognized best practices and regulatory requirements. |
Reduced Liability | Minimizes potential legal issues and liabilities related to fire incidents. |
Increased Operational Reliability | Fire-tested valves enhance reliability, reducing malfunctions during critical operations and ensuring process continuity. |
FAQs on API 607 & API 608
Q: What does “fire-safe” mean in the context of API 607?
“Fire-safe” refers to the ability of valves to maintain their integrity and functionality even in the presence of fire or high-temperature conditions. Valves that comply with API 607 standards undergo rigorous testing to ensure they can withstand extreme heat and pressure, thereby preventing catastrophic failures during fire incidents.
Q: What are the key testing requirements outlined in API 607?
API 607 mandates various tests, including fire endurance testing, thermal cycling, and pressure testing, among others. These tests assess the valve’s performance under simulated fire conditions, ensuring it can effectively control fluid flow and maintain tight shut-off even when exposed to intense heat and pressure.
Q: What is the certification process for API 608?
API-certified manufacturers can produce valves that meet API 608 standards. The certification process includes submitting relevant documents and information, undergoing audits, and conducting on-site reviews and tests.
Q: What requirements does the API 608 standard have for valve quality?
API 608 stipulates the requirements for valve materials, dimensions, design pressure, sealing performance, operation methods, etc. to ensure the safety and reliability of valves in use.
Q: Do valves have to meet API 607 or API 608?
Not all valves need to comply with these standards. Typically, valves are required to meet API 607 or API 608 for applications where there is a high risk of fire or where stringent safety standards are required.
Want To Learn More? Click Here To View Product Details!